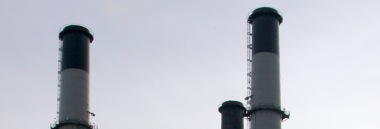
Maintenance and repair welding cases
Wear-Management offers an efficient co-operation environment between your organisation and specially selected experts.
Take advantage of our experience and our data base.
Hydropower plants:
The most common steels used for hydropower components is the martensitic 13/4
CrNi steel. This steel offers good mechanical characteristics, satisfying
machinability, weldability and considerable resistance against erosion and
cavitation. Yet, combining all these different features is a compromise to a
certain extent.
Cavitation occurs to varying degrees throughout the wide spectrum of hydraulic
machine types, sizes and ages. Cavitation produces local elastic and/or plastic
deformation of the surface and provokes surface tearing or surface fatigue.
The length of the incubation period depends on both cavitation intensity and the
material's resistance / suface finish.
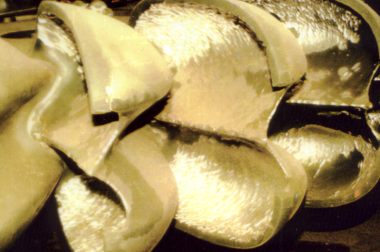
Heavily worn Pelton wheel
Sand erosion occurs to areas subject to turbulence or changes in direction.
In order to characterize the behaviour of each coating material against
sand erosion, tests were performed on specimens with a special device
developed at the Swiss Federal Institute of Technology of Lausanne.
After the first qualification with a speed of 65 m/s and an angle of
15 degrees for many different coating materials, the HVOF (WC/Co/Cr)
and Arc Spraying gave the best results. They were then used for further
experimentation in varying the speed and the angle.
Actually, there is an increased need for tailor-made coatings to improve
wear resistance of turbine components. A broad range of coating systems
is proposed such as HVOF, Plasma, Arc spraying, Welding and Cold Polymeric
Coating Systems.
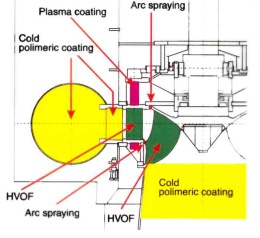
Selected coatings for Francis turbines
Increased availability and efficiency of hydropower plants and the protection
or repair of expensive components is the final objective of Wear-Management.
Surface protection technologies such as HVOF or arc spraying as well as
new materials for welding offer the possibility of optimized wear solutions.
Thermal power station
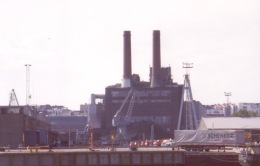
Thermal power station: Wear-Management as a key contributor to business profitability
e-service - worldwide: wear-management - free documentation
As a member of the world's premier partner in maintenance and repair welding you have access
to our world-wide e-service.
Join online: wear-management - free
documentation.
Individual Membership Annual Dues $ 140.00 or € 100.00 or CHF 140.00
No Annual Dues for Student Membership.
Guarantee yourself the peace of mind that a quality support staff is standing by to assist you when you need them.
For further information, on-site training, technical advise or project management, please do not hesitate to
contact us.
|