Welded ferrous coatings
Coating applications, both for prevention and repair, are designed to reinforce
certain specific surface properties of the workpiece: resistance to wear, heat,
corrosion, etc.
In most cases this involves the welding of dissimilar materials.
When welding dissimilar materials, the dilution must be controlled to a minimum
- using low heat input procedures.
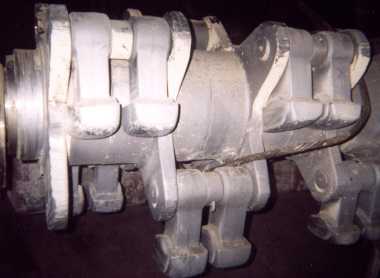
Swing hammers are subject to constant wear from impact and abrasion.
Wear and spare part management pays dividends !
Tungsten carbide type
High chromium irons
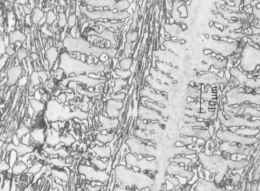
Complex alloy type
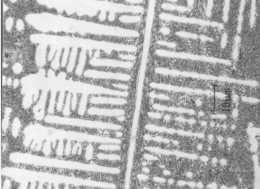
Chromium carbide type
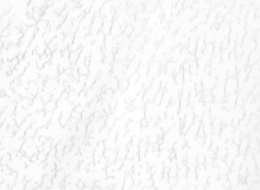
Austenitic type
Tool steels
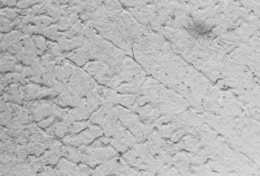
Cold working steel
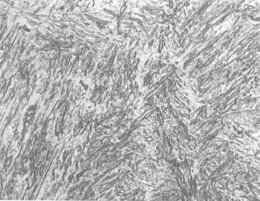
Hot working steel
Procedures
Basic wearfacing oscillation techniques
- Stringer bead: Reduced heat input, less dilution
- Weaving: MMA, Width approx. 1.5 x diam. electrode
- Straight line: Open arc, Width approx. 20 mm
Single-layer coating
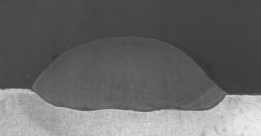
Stringer bead
Generally, maximum hardness cannot be achieved in one layer.
However some alloys can give optimum results with only one layer.
Multi-layer coating
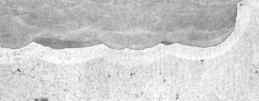
Multi-layer coating
A buttering layer may sometimes be necessary to build up or to tolerate the
dilution without cracking.
Graded coatings
Multilayers exhibiting stepwise changes of composition and/or structures are a
first approximation to continuously graded coatings.
Weld patterns
Diamond pattern
Diamond pattern and dot deposit
Waffle or cross hatch pattern
Quick dot deposits
Welded non-ferrous coatings
Nickel alloys
A first characterisation of Nickel alloys can done by a rough analyse of their composition:
Alloying elements |
|
Influence on different hardening system |
|
Influence on properties |
|
|
|
|
|
Cr |
|
Solid solution hardening Formation of carbides Sigma-phase |
|
High temperature corrosion resistance Oxidation resistance |
|
|
|
|
|
Fe |
|
Solid solution hardening |
|
|
|
|
|
|
|
C |
|
Carbide formation ( MC, M6C, M23C6 , M7C3 ) |
|
|
|
|
|
|
|
Mo |
|
Solid solution hardening Carbide formation (M6C, MC) |
|
Pitting corrosion resistance |
|
|
|
|
|
W |
|
Solid solution hardening Carbide formation (M6C, MC) |
|
|
|
|
|
|
|
Al |
|
Solid solution hardening Precipitation hardening by intermetallics γ'-Ni3Al |
|
Oxidation resistance Creep resistance |
|
|
|
|
|
Ti |
|
Solid solution hardening Precipitation hardening by intermetallics γ' Carbide formation (MC) |
|
|
Co |
|
Solid solution hardening Improve temperature stability of intermetallics γ' |
|
|
|
|
|
|
|
Ta |
|
Solid solution hardening Carbide formation |
|
|
|
|
|
|
|
Nb (Cb) |
|
Solid solution hardening Carbide formation |
|
|
|
|
|
|
|
B (low percentage) |
|
Boride formation |
|
Creep resistance |
|
|
|
|
|
Zr (low percentage) |
|
Carbide formation (MC) |
|
Creep resistance |
|
|
|
|
|
Y |
|
|
|
Oxidation resistance |
|
|
|
|
|
La |
|
|
|
Oxidation resistance |
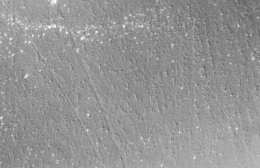
Nickel alloy
Welding processes
- Manual Metal Arc (MMA)
- MIG (Metal Inert Gas)
- Submerged Arc Welding
- PTA
Cleaning
Use stainless steel brushes, appropriate disk grinders or fine grinding wheels.
Chromium-containing nickel alloys are less susceptible to damage by sulphur, but nevertheless,
the removal of any sulphur-containing contaminants from the surface must be done before welding.
Procedure
MMA: A stringer bead approach is applied at a slow speed to build up a heavy steep-sided deposit.
A minimum of three layers is required to achieve less than 5% iron dilution.
MIG: A stringer bead approach as for Manual Metal Arc welding is applied.
In the Spray Arc Mode the dilution is somewhat less than for Manual Metal Arc Welding
but three layers of weld metal are usually necessary to be below 5% dilution after machining.
In the Short Arc and Pulsed Mode, the dilution should be less so that only two layers can be sufficient.
Submerged Arc Welding: Usually 1.6 or 2.4 mm diameter wire is used with nickel base alloys.
The most efficient use of the submerged-arc process is achieved when the torch can be oscillated.
Cobalt alloys
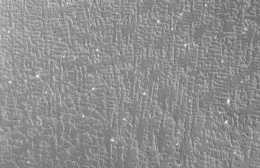
Stellite 12
Welding processes
- Manual Metal Arc (MMA)
- MIG (Metal Inert Gas)
- PTA
Base metals
see chapter steel
Safety: Arc welding
see chapter safety
Case studies
Coating of heavy components:
Improved availability and performance, optimised spare part management and
reduced use of natural resources are principal objectives.
There are hundreds of potential applications for improving the
wear approach within a production plant.
Coating of cold working tools:
In general, it is preferable to use the arc welding coating system on tools and
dies.
To produce sound coatings, correct welding procedure is necessary : process,
consumable and heat treatment are prescriped.
The base metal, dimension/shape and working conditions of the tools must be
considered when establishing procedure.
The right selection of the arc welding process has a technical and an economic
impact.
The trend is to substitute tool steels with low alloy steels, carbon steels or
even cast iron.
For welding, this implies reduction of preheating temperature and heat
treatment.
For further information, on-site training, technical advise or project management, please do not hesitate to
contact us.
|