Wear-Management leads to better use of invested capital in production plants.
It improves availability, performance and maintainability of equipment and components substantially.
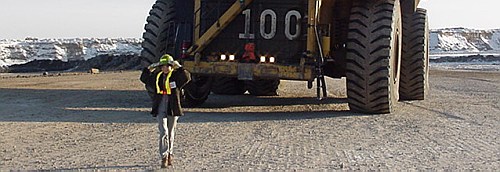
Mining.
Sustainable development
Wear-Management reduces use of natural resources through longer-lasting machinery
and components.
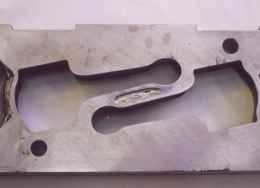
Automotive: Expensive trimming die, NiCrMo tool steel.
Result driven maintenance
A new way to progress in maintenance is to combine
- expertise and best practice,
- communication and training,
- benchmarking and networking,
- implementation and documentation.
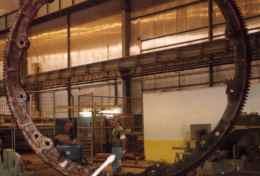
Heavy maintenance: Kiln girth repair
Price per new component: up to 1'000'000 €
Delivery time: 6 to 9 months
Down time cost: 20'000 to 30'000 € per day
Offshoring
Wear-Management promotes the development of virtual structures and projects as
well as the implementation of continuous improvement processes.
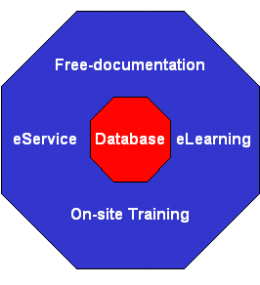
In-depth communication
The availability of on-site expertise and best practice becomes more and
more a problem.
Free (as freedom) documentation of international expertise and best practice is the most attractive
answer.
Industries:
Wear-Management sets trends - Know-how for everybody:
All documentation located on the wear-management web site is licensed under the
GNU Free Documentation
Licence. The purpose is to assure everyone the effective freedom to copy and
redistribute it, with or without modifying it, either commercially or non-commercially.
Wear-Management - free documentation
Individual Membership
As a member of the world's premier partner in maintenance and repair welding you have access
to our world-wide e-service.
Join online: wear-management - free
documentation.
Annual Dues $ 150.00 or € 150.00 or CHF 150.00
for reducing your down time and spare part costs and the promotion of sustainable development.
For further information, on-site training, technical advise or project management, please do not hesitate to
contact us.
|